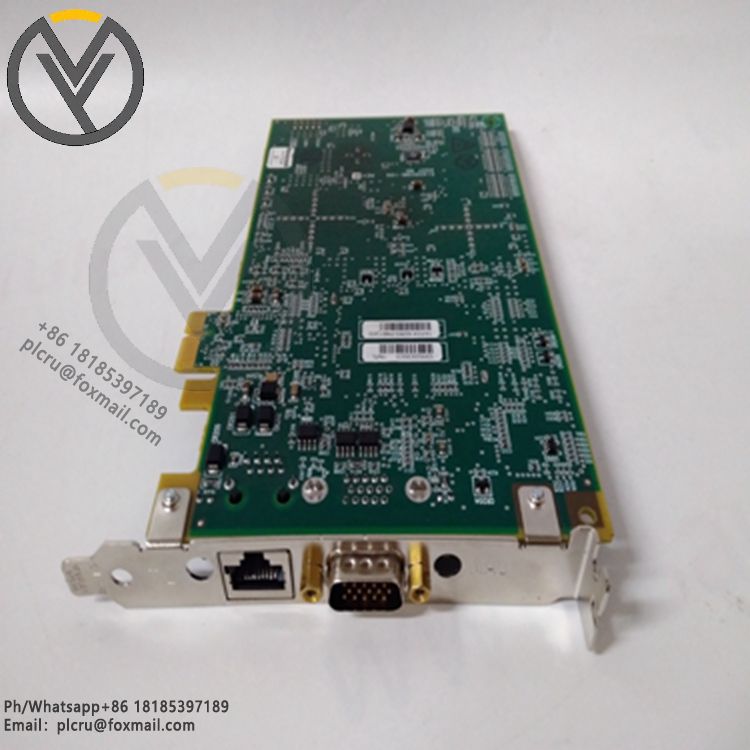
10020/1/2 | Honeywell | FSC CPU Module
Delivery time 3 days
Product origin New/used
Email plcru@foxmail.com
Mobile/wechat /WhatsApp +86 18185397189
I. Product OverviewModel: 10020/1/2Type: The central processing unit (CPU) modul
I. Product Overview
Model: 10020/1/2
Type: The central processing unit (CPU) module of the Safety Control System (FSC) belongs to the Honeywell Safety Manager or FSC (Fault Tolerant Control System) series and is specifically designed for highly reliable safety-critical applications (such as SIL3-level safety systems).
Core positioning: As the "brain" of the safety system, it is responsible for performing logical operations, safety control strategies, fault diagnosis, and data interaction with I/O modules and communication modules, ensuring that industrial processes automatically trigger safety actions (such as shutdown and alarm) in abnormal situations.
Ii. Core Functions
1. Security Architecture and reliability
Fault-tolerant design
Support Triple Modular Redundancy (TMR) or Dual Redundancy, and ensure that a single point of failure does not affect the normal operation of the system through a hardware voting mechanism (such as a three-by-two vote).
It is equipped with an internal self-diagnostic function to monitor the status of key components such as CPU, memory, and communication links in real time, with a diagnostic coverage rate (DC) of ≥99%.
Safety standard compliance
It complies with functional safety standards such as IEC 61508 (SIL3), IEC 61511 (TUV certification), and ISA 84.00.01, and is applicable to high-risk scenarios such as petroleum, chemical engineering, and nuclear power.
2. Data processing and logical execution
Processor performance:
It adopts high-performance industrial-grade microprocessors (such as PowerPC or ARM cores), supports real-time multitasking operating systems (RTOS), and the logic execution speed can reach the μs level (for example, the execution time for every thousand instructions is less than 1ms).
Supports programming languages such as Ladder Diagram (LD), Function Block Diagram (FBD), Structured Text (ST), etc., and is compatible with Honeywell Safety Builder or FSC configuration software.
Memory configuration:
Program storage area: Usually Flash ROM (≥16MB), supporting firmware upgrade and program backup.
Data storage area: RAM (≥8MB), used for real-time data caching and temporary variable storage.
3. Communication and Interface
Internal communication
The I/O module, communication module and redundant CPU module are connected through dedicated buses (such as vertical bus and horizontal bus), with a data transmission rate of ≥100Mbps and support for hot plugging (online replacement).
External communication
It is standard-equipped with 1-2 Ethernet ports (supporting Modbus TCP, Ethernet/IP or dedicated protocols), and can be optionally equipped with RS-485/RS-232 serial ports for connecting to the upper computer, SCADA system or third-party devices.
Support the OPC UA secure communication protocol to achieve data interaction with the cloud or MES system.